How regenerative braking works is a fascinating process that converts kinetic energy into usable electrical energy during braking. This innovative technology is revolutionizing transportation, significantly improving efficiency and reducing environmental impact compared to traditional braking methods. It’s more than just stopping; it’s about harnessing wasted energy.
Regenerative braking essentially reverses the flow of energy in a vehicle’s system, using the braking process to recharge the battery or other energy storage device. This allows for a more sustainable and efficient operation, crucial in electric vehicles and hybrid systems. By understanding the intricate workings of the system, we can appreciate its potential for the future of transportation.
Introduction to Regenerative Braking
Regenerative braking is a sophisticated method of energy recovery during vehicle deceleration. Instead of simply dissipating kinetic energy as heat, as in conventional braking, regenerative braking converts it back into electrical energy, which can then be stored or used to power the vehicle’s electric motor. This process significantly enhances fuel efficiency and reduces environmental impact.Unlike conventional braking systems, regenerative braking systems utilize the vehicle’s electric motor as a generator, harnessing the kinetic energy during deceleration to produce electricity.
This contrasts sharply with conventional systems that convert kinetic energy directly into heat. The recovered energy can be stored in batteries, reducing the overall energy consumption of the vehicle.
Core Principle of Regenerative Braking
Regenerative braking fundamentally relies on the principle of energy conversion. During deceleration, the kinetic energy of the vehicle is converted into electrical energy by the electric motor, which acts as a generator. This process significantly enhances fuel efficiency and reduces reliance on fossil fuels.
Difference Between Conventional and Regenerative Braking
Conventional braking systems use friction to stop the vehicle. The friction between brake pads and rotors converts kinetic energy into heat, which is then dissipated into the surrounding environment. Regenerative braking, in contrast, employs the electric motor as a generator to convert the kinetic energy into electrical energy, which can be stored or used for propulsion.
Role of Energy Recovery in Regenerative Braking
Energy recovery is the cornerstone of regenerative braking. By converting kinetic energy into electrical energy, the system captures and stores the energy that would otherwise be lost as heat. This stored energy can be used to power the vehicle’s electric motor, thus reducing the vehicle’s reliance on external energy sources like gasoline. The recovered energy contributes to enhanced fuel efficiency and reduced emissions.
Simple Analogy
Imagine a water turbine. During deceleration, the kinetic energy of the vehicle is analogous to the water flowing through the turbine. In conventional braking, this energy is lost as heat, like the water flowing into a drain. In regenerative braking, the water turns the turbine, generating electricity, analogous to the motor generating electricity from the vehicle’s kinetic energy.
Comparison of Conventional and Regenerative Braking Systems
Feature | Conventional Braking | Regenerative Braking |
---|---|---|
Energy Conversion | Kinetic energy to heat | Kinetic energy to electrical energy |
Efficiency | Lower (significant energy loss as heat) | Higher (energy recovery and reuse) |
Environmental Impact | Higher (increased reliance on fossil fuels, more emissions) | Lower (reduced reliance on fossil fuels, lower emissions) |
Components of a Regenerative Braking System
Regenerative braking, a crucial element in modern electric vehicle technology, recovers kinetic energy during deceleration. This recovered energy is then stored and reused, enhancing efficiency and reducing reliance on the primary power source. The effectiveness of this process hinges on a meticulously designed system comprised of several key components.Key components of a regenerative braking system work in concert to harness and store the kinetic energy.
The electric motor, often the heart of the system, acts as both a motor and a generator, depending on the driving or braking conditions. The system must convert the energy into a usable form for storage. This process involves careful design and selection of materials to ensure optimal performance and durability.
Electric Motor
The electric motor is the central component in the energy recovery process. When the vehicle brakes, the motor’s role transforms from driving the wheels to generating electricity. This conversion relies on the principles of electromagnetism, where the rotation of the motor’s shaft generates a current. High-efficiency electric motors, often featuring permanent magnet synchronous or induction designs, are crucial for maximum energy recovery.
These motors are designed to operate effectively across a wide range of speeds and torque demands, ensuring consistent performance during braking.
Inverter
The inverter is a crucial component that bridges the gap between the electric motor and the power storage system. It acts as a power converter, transforming the direct current (DC) generated by the motor into alternating current (AC). This conversion is necessary to match the electrical characteristics of the power storage system. Modern inverters employ advanced semiconductor devices like insulated gate bipolar transistors (IGBTs) or silicon carbide (SiC) MOSFETs, enabling efficient and fast switching between motor operation modes.
The efficiency of the inverter directly impacts the overall energy recovery effectiveness. Optimized inverter design minimizes energy losses during the conversion process.
Power Storage System
The power storage system, typically a battery pack, is responsible for storing the recovered energy. This stored energy can then be used to power the vehicle’s electrical systems or to replenish the battery’s charge. The battery’s capacity and charging/discharging characteristics influence the amount of energy that can be recovered. High-energy-density batteries, such as lithium-ion, are commonly employed in modern electric vehicles.
Their ability to store and release energy efficiently is vital for effective regenerative braking.
Control System
The control system orchestrates the entire regenerative braking process. It monitors the vehicle’s speed and braking demands, adjusting the motor’s operation accordingly. Sophisticated algorithms and sensors within the control system allow for precise control of the energy recovery process. This ensures that the braking force is optimized to maximize energy recovery while maintaining vehicle stability.
Component Name | Function | Materials Used |
---|---|---|
Electric Motor | Converts mechanical energy to electrical energy during braking; drives the wheels during acceleration. | Copper windings, permanent magnets, steel housings |
Inverter | Converts DC to AC to match the electrical characteristics of the power storage system. | Semiconductor devices (IGBTs, SiC MOSFETs), copper wiring |
Power Storage System | Stores the recovered energy for later use. | Lithium-ion cells, electrolytes, protective casings |
Control System | Monitors vehicle speed and braking demands, adjusting motor operation accordingly. | Microprocessors, sensors, control software |
The specific materials used in each component directly influence its performance characteristics. For example, the use of high-efficiency semiconductors in inverters minimizes energy losses during conversion. High-energy-density battery chemistries maximize the amount of energy that can be stored. Careful material selection ensures optimal performance, longevity, and safety.
Working Mechanisms
Regenerative braking, a crucial component of modern transportation systems, significantly enhances efficiency by converting kinetic energy into electrical energy during deceleration. This process is a key factor in reducing energy consumption and promoting sustainability. The detailed working mechanism involves a series of steps, each meticulously managed by sophisticated electronic controllers.The process of converting kinetic energy into electrical energy during braking is a crucial aspect of regenerative braking.
This transformation is facilitated by the inherent properties of the system’s components, such as electric motors, and carefully orchestrated by the electronic control system. The interplay of these elements is vital in achieving optimal energy recovery.
Step-by-Step Procedures
The regenerative braking process unfolds in a series of well-defined steps. Understanding these steps reveals the intricate mechanism behind the energy recovery process.
- During deceleration, the kinetic energy of the vehicle is converted into mechanical energy, causing the wheels to rotate. This mechanical energy is then transferred to the electric motor, which acts as a generator.
- The electric motor, now acting as a generator, converts the mechanical energy into electrical energy. This energy is fed back into the vehicle’s electrical system.
- Sophisticated electronic controllers monitor the braking process and adjust the motor’s function. These controllers regulate the amount of electrical energy generated to ensure the system’s efficiency and safety.
- The generated electrical energy is stored in the vehicle’s battery or used to power other electrical components. This energy recovery significantly reduces the demand on the primary power source.
Conversion of Kinetic Energy to Electrical Energy
Regenerative braking relies on the principle of converting kinetic energy into electrical energy. This process is fundamental to the system’s effectiveness.
- Kinetic energy, the energy of motion, is inherently present in a moving vehicle. This energy is directly proportional to the vehicle’s mass and velocity squared.
- During braking, the vehicle’s kinetic energy is reduced as it slows down. This reduction in kinetic energy is converted into electrical energy through the regenerative braking process.
- The electric motor, acting as a generator, absorbs the mechanical energy produced by the braking system, converting it into electrical energy. This electrical energy is then channeled back into the electrical system of the vehicle.
Role of Electronic Controllers
Electronic controllers play a pivotal role in the smooth and efficient operation of a regenerative braking system. These controllers are essential for optimal performance.
- Electronic controllers constantly monitor the braking process, adjusting the motor’s function in real-time to optimize energy recovery. This fine-tuning ensures the system’s efficiency and safety.
- These controllers carefully manage the generated electrical energy, ensuring it is safely stored or used to power other electrical components within the vehicle. This meticulous control is critical for the system’s effectiveness.
- They ensure the process is safe and stable, preventing damage to the system components. This includes regulating the current and voltage to prevent overloading.
Conversion of Mechanical Energy to Electrical Energy
The conversion of mechanical energy into electrical energy is a fundamental principle of regenerative braking. This process is the core function of the electric motor.
The conversion of mechanical energy to electrical energy occurs through Faraday’s law of induction.
- When the motor acts as a generator, mechanical energy from the vehicle’s braking system is applied to the rotor of the motor.
- This causes a change in magnetic flux, which, according to Faraday’s law, induces a voltage in the motor’s windings. This induced voltage results in an electrical current.
- The direction of this induced current is opposite to the current used when the motor acts as a motor. This reversal is a key aspect of regenerative braking.
Visual Representation of the Regenerative Braking Process
The following flowchart illustrates the regenerative braking process:[Insert a flowchart here. A simple flowchart showing the steps from kinetic energy to electrical energy storage, with labels for each step. The flowchart should clearly depict the role of the electronic controller and the conversion of mechanical energy to electrical energy. For example, it could have boxes for “Deceleration,” “Motor as Generator,” “Electrical Energy Generation,” “Controller Monitoring,” “Energy Storage,” etc.
Connect these boxes with arrows to show the flow.]
Types of Regenerative Braking Systems
Regenerative braking systems, a crucial component in modern transportation, vary significantly in their design and application. Understanding these differences is vital for selecting the most suitable system for a specific vehicle or application. These systems leverage the kinetic energy of motion to generate electricity, improving fuel efficiency and extending battery life in electric vehicles.Different types of regenerative braking systems are tailored to specific vehicle needs, reflecting varying degrees of complexity, performance, and efficiency.
Regenerative braking essentially captures kinetic energy and converts it back into electrical energy, which can then be used to power the vehicle. This process is quite efficient, offering a boost in fuel economy. Modern advancements, like the integration of AI in healthcare, are pushing boundaries in numerous sectors. This energy recapture mechanism in vehicles, akin to how regenerative braking works, has parallels in optimizing energy usage in other fields, highlighting the potential for broader applications.
The selection process considers the vehicle’s operating conditions, anticipated braking demands, and overall system requirements.
Classification of Regenerative Braking Systems
Regenerative braking systems are categorized based on their underlying principles and implementation strategies. These distinctions impact their performance and efficiency in different scenarios.
Induction Motor-Based Systems
Induction motor-based systems are prevalent in electric vehicles due to their robust construction and efficiency at higher speeds. These systems employ induction motors, which convert electrical energy to mechanical energy and vice-versa. This characteristic allows the motor to act as a generator during braking, recovering kinetic energy. The process is highly efficient at high speeds, making it suitable for high-speed applications like electric trains and buses.
The design’s strength lies in its ability to handle substantial braking demands during rapid deceleration, a crucial feature for heavy-duty vehicles.
Permanent Magnet Synchronous Motor (PMSM)-Based Systems
PMSM-based systems offer superior performance and efficiency, especially at lower speeds. The permanent magnets within the motor provide a constant magnetic field, facilitating more precise control over the braking process. This precision is particularly beneficial in applications requiring precise deceleration, such as hybrid electric vehicles (HEVs) and advanced electric vehicles. The system’s efficiency is often higher at lower speeds compared to induction motor-based systems.
Direct Current (DC) Motor-Based Systems
DC motor-based systems are a traditional approach, although their application in modern vehicles is less common. These systems employ DC motors, which have a simpler structure compared to other types. However, they might not offer the same level of efficiency as induction or PMSM-based systems. The system’s characteristics make them suitable for applications with relatively lower braking demands and simpler control requirements.
Comparison Table of Regenerative Braking Systems
System Type | Advantages | Disadvantages | Typical Applications |
---|---|---|---|
Induction Motor-Based | High efficiency at high speeds, robust design, capable of handling high braking demands. | Lower efficiency at lower speeds, potentially higher cost compared to DC motors. | Electric trains, buses, heavy-duty electric vehicles. |
PMSM-Based | Superior efficiency and performance at lower speeds, precise control over braking, higher efficiency at lower speeds than induction systems. | Can be more complex and expensive than induction motor systems, potentially requiring more sophisticated control mechanisms. | Hybrid electric vehicles (HEVs), advanced electric vehicles, and applications requiring precise braking control. |
DC Motor-Based | Simpler structure, relatively lower cost. | Lower efficiency compared to induction or PMSM systems, less suitable for high-speed applications. | Older electric vehicles, applications with lower braking demands. |
Energy Storage and Utilization
Regenerative braking systems effectively recapture kinetic energy, but the recovered energy must be stored and utilized for maximum benefit. This process requires specialized energy storage mechanisms to handle the fluctuating power demands and convert the captured energy into usable forms. Different methods offer varying levels of efficiency and capacity, influencing the overall performance and cost-effectiveness of the system.
Energy Storage Methods
Various energy storage technologies are employed to store the recovered energy. These methods differ in their capacity, charging/discharging rates, and cost. A crucial consideration is the ability of the storage system to handle the intermittent nature of regenerative braking, which can fluctuate significantly depending on driving conditions.
- Batteries: Lithium-ion batteries are frequently used due to their high energy density and relatively fast charging/discharging rates. They are suitable for applications requiring significant energy storage capacity. However, their lifespan and potential for degradation with repeated cycles should be considered.
- Supercapacitors: These devices offer faster charging/discharging rates than batteries, making them well-suited for situations where quick energy delivery is essential. While their energy density is lower than batteries, they excel in applications requiring frequent and rapid energy exchanges.
- Hybrid Systems: Combining batteries and supercapacitors can create a hybrid storage solution. This approach leverages the strengths of both technologies, potentially offering a balance between high energy density and fast charging/discharging capabilities. The optimal configuration depends on the specific application and its performance requirements.
Energy Storage Efficiency
The efficiency of energy storage and utilization directly impacts the overall system performance. Factors such as the conversion efficiency of the braking system, the efficiency of the storage device, and the efficiency of the energy release process all contribute to the overall energy balance. Real-world examples demonstrate that energy storage efficiency can significantly vary based on factors like the type of storage medium and the charging/discharging conditions.
Energy storage efficiency is a critical factor in determining the overall effectiveness of a regenerative braking system.
- Losses during Storage: Energy losses occur during the conversion and storage processes. These losses are a direct result of inefficiencies in the components, such as the electrical resistance in the system or the heat generated during the conversion and storage steps. Optimization strategies are employed to minimize these losses.
- Charging/Discharging Cycles: The number of charging and discharging cycles a storage device can withstand affects its longevity and energy storage efficiency over time. This is especially important for high-usage applications where the system will be repeatedly charging and discharging the stored energy.
Energy Release Process
The process of releasing the stored energy for other uses is crucial for system efficiency. This involves converting the stored energy back into electrical energy, which can then be utilized for powering various electrical components of the vehicle.
- Power Conversion: The stored energy must be converted back into electrical energy. The process involves inverters and other power electronics that efficiently transform the energy from the storage device to the appropriate voltage and frequency needed by the vehicle’s electrical system.
- System Integration: Integrating the energy release process into the vehicle’s overall electrical system is essential for smooth operation. Careful planning ensures that the energy released from the storage device effectively powers the desired components without overloading the system.
Role in Overall System Efficiency
Energy storage plays a critical role in enhancing overall system efficiency. By recovering energy during braking, the vehicle reduces its reliance on the primary power source (e.g., gasoline engine). This direct impact on fuel consumption directly translates into lower emissions and reduced operating costs.
- Reduced Fuel Consumption: The recovered energy significantly reduces the demand on the primary power source, leading to reduced fuel consumption and lower operating costs. This is especially important for electric and hybrid vehicles, where regenerative braking can dramatically enhance fuel economy.
- Enhanced Vehicle Range: By recovering and storing energy during braking, the overall driving range of an electric or hybrid vehicle is increased, improving the operational efficiency of the vehicle.
Advantages and Disadvantages of Regenerative Braking
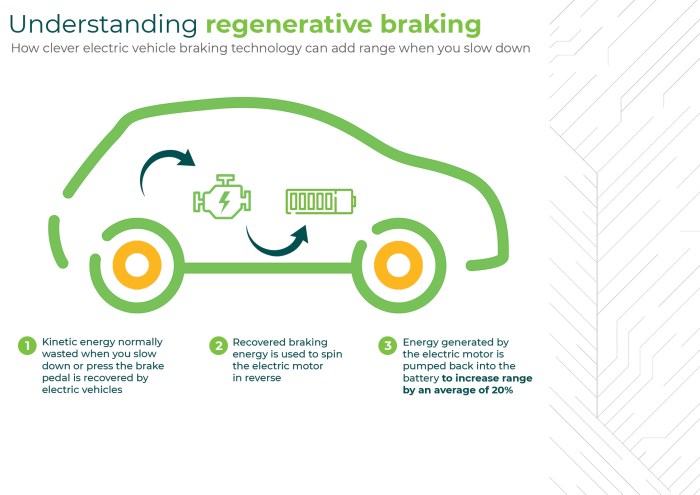
Regenerative braking, a technology that recovers energy during braking, offers significant advantages in terms of efficiency and sustainability. This method converts kinetic energy into electrical energy, which can then be reused, thereby reducing reliance on traditional braking methods. However, implementing regenerative braking systems presents certain challenges.Regenerative braking systems, while offering substantial benefits, also come with limitations. These limitations stem from the complexity of the systems and the need for specific infrastructure to accommodate the generated electricity.
Understanding both the advantages and disadvantages is crucial for evaluating the suitability of this technology in various applications.
Advantages of Regenerative Braking
Regenerative braking significantly improves energy efficiency compared to traditional friction-based braking. The recovered energy can be stored and later used to power the vehicle, reducing the overall energy consumption. This translates to reduced reliance on fossil fuels and lower operating costs over the vehicle’s lifetime. Furthermore, the reduced wear and tear on brake components results in longer component lifecycles.
- Energy Efficiency: Regenerative braking recovers kinetic energy lost during braking, substantially reducing the need for energy from the power source, leading to significant fuel savings, especially in electric vehicles.
- Environmental Impact: Reduced fuel consumption directly contributes to lower greenhouse gas emissions. This translates to a smaller carbon footprint and a more sustainable transportation system, aligning with environmental conservation goals.
- Cost Savings: Lower fuel consumption translates to lower operating costs for the vehicle owner. This financial benefit, coupled with the extended lifespan of brake components, provides a significant long-term advantage.
Disadvantages of Regenerative Braking
While regenerative braking offers numerous benefits, there are some drawbacks that need consideration. System complexity and cost are primary concerns. Furthermore, the effectiveness of regenerative braking can be influenced by factors like the vehicle’s load, the driving conditions, and the characteristics of the road surface.
- System Complexity: Regenerative braking systems require specialized components like inverters and electric motors, increasing the overall complexity of the vehicle’s electrical system. This complexity often translates to higher production costs.
- Cost: The initial cost of incorporating regenerative braking systems can be higher than traditional friction-based braking systems. This cost can be a significant barrier for some vehicle manufacturers and consumers.
- Limitations in Applications: Regenerative braking is most effective in situations with consistent deceleration, such as highway driving. Its efficiency can be reduced on hilly terrain or during rapid deceleration events.
Table of Advantages and Disadvantages
Aspect | Advantages | Disadvantages |
---|---|---|
Energy Efficiency | Significant reduction in energy consumption | Performance may be reduced in certain driving conditions |
Environmental Impact | Lower greenhouse gas emissions and reduced reliance on fossil fuels | Requires specific infrastructure for energy storage and utilization |
Cost Savings | Lower operating costs and longer component lifespan | Higher initial system cost |
System Complexity | Advanced technology and potential for increased system failures | Higher maintenance and repair costs |
Environmental Benefits
Regenerative braking significantly contributes to sustainable transportation by reducing the reliance on fossil fuels and lowering greenhouse gas emissions. This reduction in emissions has a positive impact on air quality and global climate change mitigation. The technology’s ability to recover energy translates to a more environmentally friendly transportation solution.
Challenges and Limitations
The effectiveness of regenerative braking systems varies across different vehicle types. Electric vehicles often benefit more significantly due to their inherent electrical systems. Hybrid vehicles also incorporate this technology but with limitations. Internal combustion engine vehicles have inherent limitations in adapting regenerative braking due to the lack of an electric powertrain.
Applications and Examples: How Regenerative Braking Works
Regenerative braking, a crucial component of modern transportation systems, offers significant advantages in various applications. Its ability to recapture kinetic energy during braking and return it to the power system enhances efficiency and reduces reliance on traditional braking methods. This technology is particularly valuable in situations where energy conservation is paramount.Regenerative braking systems are effectively integrated into a diverse range of vehicles and power systems, significantly impacting their performance and environmental footprint.
The varied applications and benefits are highlighted in the following sections.
Electric Vehicles (EVs)
Regenerative braking is fundamental to the operation of electric vehicles. By converting kinetic energy into electrical energy, EVs can recover a substantial portion of the energy lost during deceleration. This recuperated energy is then stored in the vehicle’s battery, extending its range and reducing the overall energy consumption. A notable benefit is the reduced strain on the battery, leading to longer battery life.
For example, Tesla vehicles feature sophisticated regenerative braking systems that provide varying levels of braking force, tailored to the driving situation.
Hybrid Electric Vehicles (HEVs)
HEVs utilize regenerative braking to improve fuel efficiency. The system captures kinetic energy during braking and stores it in a battery or other energy storage device. This stored energy can be used to power the vehicle’s electric motor, reducing the load on the internal combustion engine. This contributes to improved fuel economy and reduced emissions. For instance, Toyota Prius models demonstrate the practical application of regenerative braking in HEVs, improving fuel efficiency and reducing tailpipe emissions.
Trains
Regenerative braking is increasingly employed in electric and hybrid trains. These systems allow trains to recapture kinetic energy during deceleration, storing it in the power system. This recovered energy can be used to power other trains or to reduce the strain on the power grid. High-speed rail systems are particularly well-suited for regenerative braking due to the high speeds and frequent braking cycles.
Examples include various high-speed rail lines globally, where regenerative braking systems are essential for operational efficiency and environmental sustainability.
Table of Applications and Benefits
Application | Key Benefits |
---|---|
Electric Vehicles | Extended range, reduced battery wear, improved performance |
Hybrid Electric Vehicles | Enhanced fuel economy, reduced emissions, improved efficiency |
Trains | Reduced energy consumption, minimized strain on power grids, increased operational efficiency |
Design Considerations for Regenerative Braking Systems
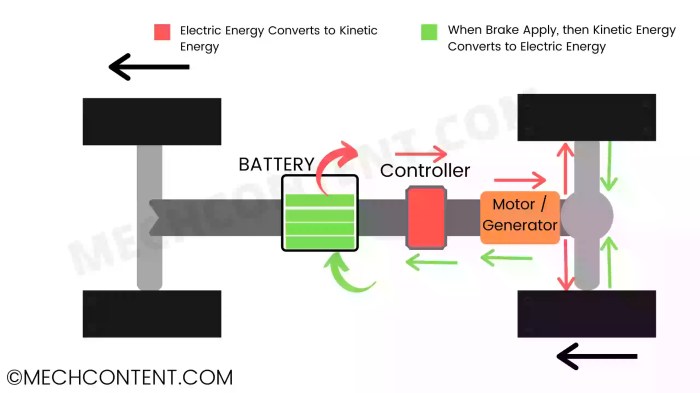
Regenerative braking systems offer a compelling approach to energy recovery in transportation applications, notably in electric vehicles. Optimizing these systems necessitates a comprehensive understanding of key design factors. Careful consideration of these aspects directly impacts the system’s efficiency, capacity, and overall performance.Effective regenerative braking systems require a meticulous balance of various design elements. The system’s ability to handle power fluctuations and energy recovery during braking is crucial.
Design considerations extend beyond the hardware components to encompass control mechanisms and materials selection, all playing critical roles in the overall performance and longevity of the system.
System Capacity and Power Handling
System capacity, a critical design consideration, dictates the amount of energy that the system can recover during braking. High-capacity systems are essential for applications demanding substantial energy recuperation, such as high-speed trains or heavy-duty electric trucks. Power handling capability is equally important, as it determines the maximum power that the system can process during regeneration. This involves careful consideration of the electrical components’ capacity to withstand the fluctuating power demands associated with braking.
Overloading these components could lead to damage or malfunction.
Control Mechanisms
The control mechanisms within a regenerative braking system play a pivotal role in optimizing energy recovery and ensuring safe operation. Sophisticated control algorithms are crucial for adapting to varying driving conditions and maximizing energy capture. These algorithms must dynamically adjust the braking intensity to match the vehicle’s speed and the energy recovery capability of the system. This adaptive control allows for precise regulation of energy flow and prevents overcharging or damaging the energy storage system.
Optimization Techniques for Energy Recovery
Maximizing energy recovery involves several optimization techniques. One approach involves calibrating the braking system to specific vehicle parameters, such as weight, speed, and load. Accurate calculations and precise control of the braking process can significantly enhance the system’s energy recovery efficiency. This can be achieved through real-time data analysis and predictive modeling, which allows for optimal energy harvesting.
Materials Used in Design
The choice of materials directly impacts the system’s performance and lifespan. High-strength and lightweight materials are crucial for the mechanical components, enabling the system to withstand stress and maintain a compact design. Electrical components, such as conductors and insulators, must have high conductivity and excellent insulation properties to handle the high currents generated during regeneration. Consideration must be given to the materials’ resistance to wear, corrosion, and temperature fluctuations to ensure the long-term reliability of the system.
Design Principles Illustration
Imagine a regenerative braking system in an electric car. A motor acts as both a generator and a motor, converting kinetic energy into electrical energy during braking. This energy is then fed into the battery, recharging it. The control system regulates the flow of electricity, ensuring efficient charging and preventing overcharging. The system’s components are carefully chosen for their specific properties, like high-strength materials for durability and low-resistance materials for efficient power transfer.
The design incorporates advanced control algorithms for adaptive braking, maximizing energy recovery across a range of driving conditions. A robust cooling system ensures the components operate within their temperature limits, preventing damage. The system’s overall design prioritizes efficiency, safety, and longevity.
Regenerative braking essentially captures kinetic energy, converting it back into electricity. This process, similar to how a dynamo works, is crucial for efficiency in vehicles. The future of blockchain, as detailed in this article Future of blockchain , might offer innovative solutions for managing and optimizing the energy grids that power these systems. Ultimately, advancements in regenerative braking technology will continue to play a significant role in a sustainable transportation future.
Future Trends and Developments
Regenerative braking systems are rapidly evolving, driven by the need for improved fuel efficiency and reduced environmental impact. The future holds significant potential for advancements in these systems, particularly in integrating them with other technologies and optimizing their energy recovery efficiency. This section explores these promising developments and their potential impact across various transportation sectors.The increasing demand for sustainable transportation solutions is fueling innovation in regenerative braking.
Engineers are focusing on maximizing energy recovery and minimizing energy losses, leading to more efficient braking systems. This, in turn, translates to reduced emissions and enhanced fuel economy, aligning with global environmental targets.
Potential for Improving Energy Recovery Efficiency
Enhanced energy recovery hinges on several key factors. Advanced control algorithms play a crucial role in optimizing the braking process, enabling the system to capture more kinetic energy during deceleration. Furthermore, improvements in the design and materials of the energy storage components, such as batteries and supercapacitors, are essential for maximizing energy density and minimizing energy losses during storage and discharge.Another area of focus is the development of more sophisticated power electronics.
These components are critical in converting the captured energy to a usable form, with higher efficiency levels translating to better overall performance. Moreover, the integration of smart grids and energy management systems could significantly improve the utilization of recovered energy, potentially feeding it back into the broader electrical grid.
Integration of Advanced Technologies, How regenerative braking works
The integration of advanced technologies is transforming regenerative braking systems. The combination of artificial intelligence (AI) and machine learning (ML) algorithms allows for dynamic adaptation to varying driving conditions, further enhancing energy recovery. These algorithms can predict braking patterns and adjust the system’s operation in real-time, maximizing energy capture.Moreover, the development of advanced sensors and actuators provides precise control over the braking process, leading to a more refined and efficient energy recovery process.
For instance, sophisticated sensors can monitor vehicle speed, acceleration, and road conditions, enabling the system to optimize braking strategies. Similarly, the implementation of advanced actuators can precisely regulate the braking force and ensure optimal energy recovery.
Future Adoption and Potential Applications
The adoption of regenerative braking is projected to increase across various transportation sectors, including automobiles, trains, and even aircraft. In the automotive sector, the shift towards electric vehicles (EVs) and hybrid electric vehicles (HEVs) is accelerating the integration of regenerative braking systems. Similarly, in the rail sector, high-speed rail networks are adopting these systems to reduce energy consumption and minimize environmental impact.
“Regenerative braking is poised to become an integral component in future transportation systems, contributing significantly to sustainable mobility.”
The potential applications extend beyond these traditional sectors. The incorporation of regenerative braking in drones and other aerial vehicles could enhance their operational efficiency and range, and the technology’s application in maritime transport is also being explored. In essence, the future of regenerative braking is intertwined with the advancement of sustainable transportation solutions across diverse sectors.
Predictions about Future Adoption
Based on current trends and advancements, regenerative braking is expected to become increasingly prevalent in transportation systems. The growing focus on environmental sustainability and the advancements in battery technology are key factors driving this adoption. The implementation of incentives and regulations in various jurisdictions further supports the widespread use of regenerative braking systems.Examples include government mandates for EVs and incentives for vehicle manufacturers incorporating regenerative braking in their models.
The rising cost of fossil fuels and increasing awareness of environmental issues are also driving the adoption of regenerative braking systems, as seen in the growing market share of hybrid and electric vehicles.
Final Thoughts
In summary, regenerative braking is a sophisticated energy-recovery system that’s changing how we approach vehicle design and operation. By efficiently converting kinetic energy into electrical energy during braking, it reduces reliance on traditional energy sources and lowers environmental impact. This process is central to the advancement of sustainable transportation and has the potential to revolutionize the industry in the years ahead.
FAQ Compilation
How does regenerative braking work in different types of vehicles?
The fundamental principle remains the same, but the specific components and implementation may vary. Electric vehicles often use electric motors as generators, while hybrid vehicles might integrate regenerative braking into their existing systems. Trains also use similar principles, but with different energy storage and conversion methods.
What are the limitations of regenerative braking systems?
While highly efficient, regenerative braking systems can face challenges in extreme conditions or with high braking forces. Also, the complexity of the system and cost of implementation can be factors to consider in certain applications.
What are the environmental benefits of regenerative braking?
Regenerative braking significantly reduces reliance on fossil fuels by recovering energy during braking. This lowers greenhouse gas emissions and promotes cleaner transportation, contributing to a more sustainable future.
How does regenerative braking compare to traditional braking methods in terms of efficiency?
Regenerative braking significantly outperforms traditional methods by converting kinetic energy into usable electrical energy. This results in higher overall efficiency and a reduction in wasted energy, which is a substantial advantage.